A fuel cell is an
electrochemical cell that converts a source fuel into an electrical
current. It generates electricity inside a cell through reactions
between a fuel and an oxidant, triggered in the presence of an
electrolyte. The reactants flow into the cell, and the reaction products
flow out of it, while the electrolyte remains within it. Fuel cells can
operate virtually continuously as long as the necessary flows are
maintained.
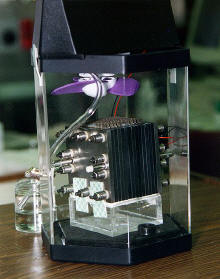
Direct-methanol fuel cell. The actual fuel cell stack is the
layered cube shape in the center of the image
Fuel cells are different from conventional electrochemical cell
batteries in that they consume reactant from an external source,
which must be replenished
– a
thermodynamically open system. By contrast, batteries store
electrical energy chemically and hence represent a thermodynamically
closed system.
Many combinations of fuels and oxidants are possible. A hydrogen fuel
cell uses
hydrogen as its fuel and oxygen
(usually from air) as its oxidant. Other fuels include
hydrocarbons and alcohols.
Other oxidants include
chlorine and
chlorine dioxide.
Design
Fuel cells come in many varieties; however, they all work in the same
general manner. They are made up of three segments which are sandwiched
together: the anode, the electrolyte, and the cathode. Two chemical
reactions occur at the interfaces of the three different segments. The
net result of the two reactions is that fuel is consumed, water or
carbon dioxide is created, and an electrical current is created, which
can be used to power electrical devices, normally referred to as the
load.
At the anode a catalyst oxidizes the fuel, usually hydrogen, turning
the fuel into a positively charged ion and a negatively charged
electron. The electrolyte is a substance specifically designed so ions
can pass through it, but the electrons cannot. The freed electrons
travel through a wire creating the electrical current. The ions travel
through the electrolyte to the cathode. Once reaching the cathode, the
ions are reunited with the electrons and the two react with a third
chemical, usually oxygen, to create water or carbon dioxide.
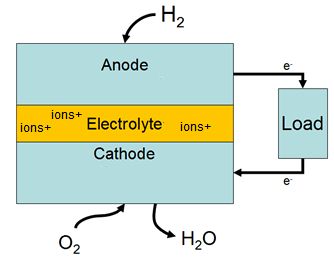
A block diagram of a fuel cell
The most important design features in a fuel cell are:
- The electrolyte substance. The electrolyte substance usually
defines the type of fuel cell.
- The fuel that is used. The most common fuel is hydrogen.
- The anode catalyst, which breaks down the fuel into electrons and
ions. The anode catalyst is usually made up of very fine platinum
powder.
- The cathode catalyst, which turns the ions into the waste
chemicals like water or carbon dioxide. The cathode catalyst is often
made up of nickel.
A typical fuel cell produces a voltage from 0.6 V to 0.7 V at full
rated load. Voltage decreases as current increases, due to several
factors:
-
Activation loss
- Ohmic loss (voltage
drop due to resistance of the cell components and interconnects)
- Mass transport loss (depletion of reactants at catalyst sites
under high loads, causing rapid loss of voltage).
To deliver the desired amount of energy, the fuel cells can be
combined in
series and parallel circuits, where series yields higher voltage,
and parallel allows a higher
current to be supplied. Such a design is called a fuel cell stack.
Further, the cell surface area can be increased, to allow stronger
current from each cell.
Proton
exchange fuel cells
In the archetypal hydrogen–oxygen
proton exchange membrane fuel cell (PEMFC) design, a
proton-conducting polymer membrane, (the
electrolyte), separates the anode and cathode
sides. This was called a "solid polymer electrolyte fuel cell" (SPEFC)
in the early 1970s, before the proton exchange mechanism was
well-understood. (Notice that "polymer electrolyte membrane" and "proton
exchange mechanism" result in the same
acronym.)
On the anode side, hydrogen diffuses to the anode catalyst where it
later dissociates into protons and electrons. These protons often react
with oxidants causing them to become what is commonly referred to as
multi-facilitated proton membranes. The protons are conducted through
the membrane to the cathode, but the electrons are forced to travel in
an external circuit (supplying power) because the membrane is
electrically insulating. On the cathode catalyst, oxygen
molecules react with the electrons (which have traveled through the
external circuit) and protons to form water — in this example, the only
waste product, either liquid or
vapor.
In addition to this pure hydrogen type, there are
hydrocarbon fuels for fuel cells, including
diesel,
methanol and chemical hydrides. The waste
products with these types of fuel are
carbon dioxide and water.
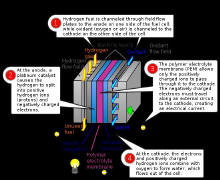
Construction of a high temperature
PEMFC: Bipolar plate as
electrode with in-milled gas channel structure, fabricated
from conductive
plastics (enhanced with
carbon nanotubes for more conductivity);
Porous carbon papers; reactive layer, usually on the
polymer membrane applied; polymer membrane.
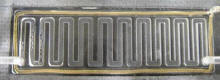
Condensation of water produced by a PEMFC on the air channel
wall. The gold wire around the cell ensures the collection of
electric current.
The materials used in fuel cells differ by type. In a typical
membrane electrode assembly (MEA), the electrode–bipolar
plates are usually made of metal, nickel
or
carbon nanotubes, and are coated with a
catalyst (like
platinum,
nano iron powders or
palladium) for higher efficiency.
Carbon paper separates them from the electrolyte. The electrolyte
could be
ceramic or a
membrane.
Proton exchange membrane fuel cell design issues
- Costs. In 2002, typical fuel cell systems cost US$1000 per
kilowatt of electric power output. In 2009, the Department of Energy
reported that 80-kW automotive fuel cell system costs in volume
production (projected to 500,000 units per year) are $61 per kilowatt. The goal is $35 per kilowatt. In 2008 UTC Power has 400 kW
stationary fuel cells for $1,000,000 per 400 kW installed costs. The
goal is to reduce the cost in order to compete with current market
technologies including gasoline internal combustion engines. Many
companies are working on techniques to reduce cost in a variety of
ways including reducing the amount of platinum needed in each
individual cell.
Ballard Power Systems have experiments with a catalyst enhanced
with
carbon silk which allows a 30% reduction (1 mg/cm² to 0.7 mg/cm²)
in platinum usage without reduction in performance.
Monash University,
Melbourne uses
PEDOT as a cathode.
- The production costs of the PEM (proton
exchange membrane). The Nafion
membrane currently costs $566/m². In 2005 Ballard Power Systems
announced that its fuel cells will use Solupor, a porous
polyethylene film patented by
DSM.
- Water and air management
(in PEMFCs). In this type of fuel cell, the membrane must be hydrated,
requiring water to be evaporated at precisely the same rate that it is
produced. If water is evaporated too quickly, the membrane dries,
resistance across it increases, and eventually it will crack, creating
a gas "short circuit" where hydrogen and oxygen combine directly,
generating heat that will damage the fuel cell. If the water is
evaporated too slowly, the electrodes will flood, preventing the
reactants from reaching the catalyst and stopping the reaction.
Methods to manage water in cells are being developed like
electroosmotic pumps focusing on flow control. Just as in a
combustion engine, a steady ratio between the reactant and oxygen is
necessary to keep the fuel cell operating efficiently.
- Temperature management. The same temperature must be maintained
throughout the cell in order to prevent destruction of the cell
through
thermal loading. This is particularly challenging as the 2H2
+ O2 -> 2H2O reaction is highly exothermic, so a
large quantity of heat is generated within the fuel cell.
- Durability,
service life, and special requirements for some type of cells.
Stationary fuel cell applications typically require more than
40,000 hours of reliable operation at a temperature of -35 °C to 40 °C
(-31 °F to 104 °F), while automotive fuel cells require a 5,000 hour
lifespan (the equivalent of 150,000 miles) under extreme temperatures.
Current
service life is 7,300 hours under cycling conditions.
Automotive engines must also be able to start reliably at -30 °C (-22
°F) and have a high power to volume ratio (typically 2.5 kW per
liter).
- Limited
carbon monoxide tolerance of the cathode.
High
temperature fuel cells
SOFC
A
solid oxide fuel cell (SOFC) is extremely advantageous “because of a
possibility of using a wide variety of fuel”. Unlike most other fuel
cells which only use hydrogen, SOFCs can run on hydrogen, butane,
methanol, and other petroleum products. The different fuels each have
their own chemistry.
For methanol fuel cells, on the anode side, a catalyst breaks
methanol and water down to form carbon dioxide, hydrogen ions, and free
electrons. The hydrogen ions move across the electrolyte to the cathode
side, where they react with oxygen to create water. A load connected
externally between the anode and cathode completes the electrical
circuit. Below are the chemical equations for the reaction:
Anode Reaction: CH3OH + H2O → CO2
+ 6H+ + 6e-
Cathode Reaction: 3/2 O2 + 6H+ + 6e-
→ 3H2O
Overall Reaction: CH3OH + 3/2 O2 → CO2
+ 2H2O + electrical energy
At the anode SOFCs can use nickel or other catalysts to break apart
the methanol and create hydrogen ions and CO2. A solid called
yttria stabilized zirconia (YSZ) is used as the electrolyte. Like all
fuel cell electrolytes YSZ is conductive to ions, allowing them to pass
from the anode to cathode, but is non-conductive to electrons. YSZ is a
durable solid and is advantageous in large industrial systems. Although
YSZ is a good ion conductor, it only works at very high temperatures.
The standard operating temperature is about 950oC. Running the fuel cell
at such a high temperature easily breaks down the methane and oxygen
into ions. A major disadvantage of the SOFC, as a result of the high
heat, is that it “places considerable constraints on the materials which
can be used for interconnections”. Another disadvantage
of running the cell at such a high temperature is that other unwanted
reactions may occur inside the fuel cell. It is common for carbon dust,
graphite, to build up on the anode, preventing the fuel from reaching
the catalyst. Much research is currently being done to find alternatives
to YSZ that will carry ions at a lower temperature.
MCFC
Molten carbonate fuel cells (MCFCs) operate in a similar manner,
except the electrolyte consists of liquid (molten) carbonate, which is a
negative ion and an oxidizing agent. Because the electrolyte loses
carbonate in the oxidation reaction, the carbonate must be replenished
through some means. This is often performed by recirculating the carbon
dioxide from the oxidation products into the cathode where it reacts
with the incoming air and reforms carbonate.
Unlike proton exchange fuel cells, the catalysts in SOFCs and MCFCs
are not poisoned by carbon monoxide, due to much higher
operating temperatures. Because the oxidation reaction occurs in the
anode, direct utilization of the carbon monoxide is possible. Also,
steam produced by the oxidation reaction can
shift carbon monoxide and
steam reform hydrocarbon fuels inside the anode. These reactions can
use the same catalysts used for the electrochemical reaction,
eliminating the need for an external fuel reformer.
MCFC can be used for reducing the CO2 emission from coal
fired power plants
as well as gas turbine power plants.
History
The principle of the fuel cell was discovered by German scientist
Christian Friedrich Schönbein in 1838 and published in one of the
scientific magazines of the time.
Based on this work, the first fuel cell was demonstrated by Welsh
scientist and barrister Sir
William Robert Grove in the February 1839 edition of the
Philosophical Magazine and Journal of Science
and later sketched, in 1842, in the same journal.
The fuel cell he made used similar materials to today's
phosphoric-acid fuel cell.
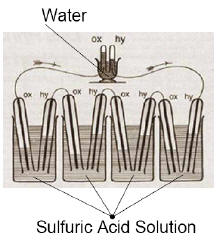
Sketch of William Grove's 1839 fuel cell
In 1955, W. Thomas Grubb, a chemist working for the General Electric
Company (GE),
further modified the original fuel cell design by using a sulphonated
polystyrene ion-exchange membrane as the electrolyte. Three years later
another GE chemist, Leonard Niedrach, devised a way of depositing
platinum onto the membrane, which served as catalyst for the necessary
hydrogen oxidation and oxygen reduction reactions. This became known as
the 'Grubb-Niedrach fuel cell'. GE went on to develop this technology
with NASA and McDonnell Aircraft, leading to its use during
Project Gemini. This was the first commercial use of a fuel cell. It
wasn't until 1959 that British engineer
Francis Thomas Bacon successfully developed a 5 kW stationary fuel
cell. In 1959, a team led by Harry Ihrig built a 15 kW fuel cell tractor
for Allis-Chalmers which was demonstrated across the US at state fairs.
This system used potassium hydroxide as the electrolyte and
compressed hydrogen and oxygen as the reactants. Later in 1959,
Bacon and his colleagues demonstrated a practical five-kilowatt unit
capable of powering a welding machine. In the 1960s, Pratt and Whitney
licensed Bacon's U.S. patents for use in the U.S. space program to
supply electricity and drinking water (hydrogen and oxygen being readily
available from the spacecraft tanks).
United Technologies Corporation's UTC
Power subsidiary was the first company to manufacture and
commercialize a large, stationary fuel cell system for use as a
co-generation power plant in hospitals, universities and large
office buildings. UTC Power continues to market this fuel cell as the
PureCell 200, a 200 kW system (although soon to be replaced by a
400 kW version, expected for sale in late 2009).
UTC Power continues to be the sole supplier of fuel cells to NASA for
use in space vehicles, having supplied the
Apollo missions,
and currently the
Space Shuttle program, and is developing fuel cells for automobiles,
buses, and cell phone towers; the company has demonstrated the first
fuel cell capable of starting under freezing conditions with its
proton exchange membrane automotive fuel cell.
Fuel cell efficiency
The efficiency of a fuel cell is dependent on the amount of power
drawn from it. Drawing more power means drawing more current, which
increases the losses in the fuel cell. As a general rule, the more power
(current) drawn, the lower the efficiency. Most losses manifest
themselves as a voltage drop in the cell, so the efficiency of a cell is
almost proportional to its voltage. For this reason, it is common to
show graphs of voltage versus current (so-called polarization curves)
for fuel cells. A typical cell running at 0.7 V has an efficiency of
about 50%, meaning that 50% of the energy content of the hydrogen is
converted into electrical energy; the remaining 50% will be converted
into heat. (Depending on the fuel cell system design, some fuel might
leave the system non-reacted, constituting an additional loss.)
For a hydrogen cell operating at standard conditions with no reactant
leaks, the efficiency is equal to the cell voltage divided by 1.48 V,
based on the
enthalpy, or heating value, of the reaction. For the same cell, the
second law efficiency is equal to cell voltage divided by 1.23 V.
(This voltage varies with fuel used, and quality and temperature of the
cell.) The difference between these numbers represents the difference
between the reaction's
enthalpy and
Gibbs free energy. This difference always appears as heat, along
with any losses in electrical conversion efficiency.
Fuel cells do not operate on a thermal cycle. As such, they are not
constrained, as combustion engines are, in the same way by thermodynamic
limits, such as
Carnot cycle efficiency.
At times this is misrepresented by saying that fuel cells are exempt
from the laws of thermodynamics, because most people think of
thermodynamics in terms of combustion processes (enthalpy
of formation). The laws of thermodynamics also hold for chemical
processes (Gibbs
free energy) like fuel cells, but the maximum theoretical efficiency
is higher (83% efficient at 298K in the case of hydrogen/oxygen
reaction) than the
Otto cycle thermal efficiency (60% for compression ratio of 10 and
specific heat ratio of 1.4). Comparing limits imposed by thermodynamics
is not a good predictor of practically achievable efficiencies. Also, if
propulsion is the goal, electrical output of the fuel cell has to still
be converted into mechanical power with another efficiency drop. In
reference to the exemption claim, the correct claim is that the
"limitations imposed by the second law of thermodynamics on the
operation of fuel cells are much less severe than the limitations
imposed on conventional energy conversion systems".
Consequently, they can have very high efficiencies in converting
chemical energy to
electrical energy, especially when they are operated at low power
density, and using pure hydrogen and oxygen as reactants.
It should be underlined that fuel cell (especially high temperature)
can be used as a heat source in conventional heat engine (gas turbine
system). In this case the ultra high efficiency is predicted (above
70%).
In practice
For a fuel cell operating on air, losses due to the air supply system
must also be taken into account. This refers to the pressurization of
the air and dehumidifying it. This reduces the efficiency significantly
and brings it near to that of a compression ignition engine. Furthermore
fuel cell efficiency decreases as load increases.
The tank-to-wheel efficiency of a
fuel cell vehicle is about 45% at low loads and shows average values
of about 36% when a driving cycle like the NEDC (New
European Driving Cycle) is used as test procedure.
The comparable NEDC value for a Diesel vehicle is 22%. In 2008 Honda
released a fuel cell electric vehicle (the
Honda FCX Clarity) with fuel stack claiming a 60% tank-to-wheel
efficiency.
It is also important to take losses due to fuel production,
transportation, and storage into account. Fuel cell vehicles running on
compressed hydrogen may have a power-plant-to-wheel efficiency of 22% if
the hydrogen is stored as high-pressure gas, and 17% if it is stored as
liquid hydrogen.
In addition to the production losses, over 70% of US' electricity used
for hydrogen production comes from
thermal power, which only has an efficiency of 33% to 48%, resulting
in a net increase in carbon dioxide production by using hydrogen in
vehicles.
Fuel cells cannot store energy like a battery, but in some
applications, such as stand-alone power plants based on discontinuous
sources such as
solar or
wind power, they are combined with
electrolyzers and storage systems to form an energy storage system.
The overall efficiency (electricity to hydrogen and back to electricity)
of such plants (known as round-trip efficiency) is between 30 and
50%, depending on conditions.
While a much cheaper
lead-acid battery might return about 90%, the electrolyzer/fuel cell
system can store indefinite quantities of hydrogen, and is therefore
better suited for long-term storage.
Solid-oxide fuel cells produce exothermic heat from the recombination
of the oxygen and hydrogen. The ceramic can run as hot as 800 degrees
Celsius. This heat can be captured and used to heat water in a
micro combined heat and power (m-CHP) application. When the heat is
captured, total efficiency can reach 80-90% at the unit, but does not
consider production and distribution losses. CHP units are being
developed today for the European home market.
Fuel cell
applications
Power
Fuel cells are very useful as power sources in remote locations, such
as spacecraft, remote weather stations, large parks, rural locations,
and in certain military applications. A fuel cell system running on
hydrogen can be compact and lightweight, and have no major moving parts.
Because fuel cells have no moving parts and do not involve combustion,
in ideal conditions they can achieve up to 99.9999% reliability.
This equates to around one minute of down time in a two year period.
Since electrolyzer systems do not store fuel in themselves, but
rather rely on external storage units, they can be successfully applied
in large-scale energy storage, rural areas being one example. In this
application, batteries would have to be largely oversized to meet the
storage demand, but fuel cells only need a larger storage unit
(typically cheaper than an electrochemical device).
One such pilot program is operating on Stuart Island in Washington
State. There the Stuart Island Energy Initiative
has built a complete, closed-loop system: Solar panels power an
electrolyzer which makes hydrogen. The hydrogen is stored in a 500
gallon tank at 200 PSI, and runs a ReliOn fuel cell to provide full
electric back-up to the off-the-grid residence.
Cogeneration
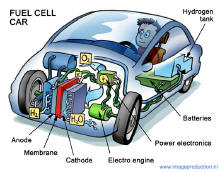
Configuration of components in a fuel cell car.
Micro combined heat and power (MicroCHP) systems such as
home fuel cells and
cogeneration for office buildings and factories are in mass
production phase. The system generates constant electric power (selling
excess power back to the grid when it is not consumed), and at the same
time produces hot air and water from the waste heat. MicroCHP is usually
less than 5 kWe for a
home fuel cell or small business.
A lower fuel-to-electricity conversion efficiency is tolerated
(typically 15-20%), because most of the energy not converted into
electricity is utilized as heat. Some heat is lost with the exhaust gas
just as in a normal furnace,
so the combined heat and power efficiency is still lower than 100%,
typically around 80%. In terms of exergy
however, the process is inefficient, and one could do better by
maximizing the electricity generated and then using the electricity to
drive a heat
pump.
Phosphoric-acid fuel cells (PAFC) comprise the largest segment of
existing CHP products worldwide and can provide combined efficiencies
close to 90%
(35-50% electric + remainder as thermal)
Molten-carbonate fuel cells have also been installed in these
applications, and
solid-oxide fuel cell prototypes exist.
Hydrogen transportation and refueling
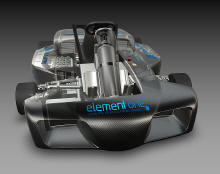
Element One fuel cell vehicle |
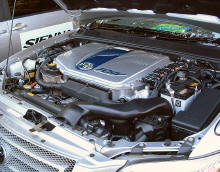
Toyota FCHV PEM FC fuel cell vehicle. |
Land vehicles
In 2003 President George Bush proposed the Hydrogen Fuel Initiative (HFI),
which was later implemented by legislation through the 2005 Energy
Policy Act and the 2006 Advanced Energy Initiative. These aimed at
further developing hydrogen fuel cells and its infrastructure
technologies with the ultimate goal to produce commercial fuel cell
vehicles by 2020. By 2008, the U.S. had contributed 1 billion dollars to
this project.
In May 2009, however, the
Obama Administration announced that it will "cut off funds" for the
development of fuel cell
hydrogen vehicles, since other vehicle technologies will lead to
quicker reduction in emissions in a shorter time. The
US Secretary of Energy explained that hydrogen vehicles "will not
be practical over the next 10 to 20 years", and also mentioned the
challenges involved in the development of the required infrastructure to
distribute hydrogen fuel. Nevertheless, the U.S. government will
continue to fund research related to
stationary fuel cells.
The
National Hydrogen Association and the
U.S. Fuel Cell Council criticized this decision arguing that "...the
cuts proposed in the DOE hydrogen and fuel cell program threaten to
disrupt commercialization of a family of technologies that are showing
exceptional promise and beginning to gain market traction."
There are numerous prototype or production cars and buses based on
fuel cell technology being researched or manufactured by motor car
manufacturers.
The GM 1966 Electrovan was the automotive industry's first attempt at
an automobile powered by a hydrogen fuel cell. The Electrovan, which
weighed more than twice as much as a normal van, could travel up to
70 mph for 30 seconds.
The 2001
Chrysler Natrium used its own on-board hydrogen processor. It
produces hydrogen for the fuel cell by reacting
sodium borohydride fuel with Borax,
both of which Chrysler claimed were naturally occurring in great
quantity in the United States.
The hydrogen produces electric power in the fuel cell for near-silent
operation and a range of 300 miles without impinging on passenger space.
Chrysler also developed vehicles which separated hydrogen from
gasoline in the vehicle, the purpose being to reduce emissions without
relying on a nonexistent hydrogen infrastructure and to avoid large
storage tanks.
In 2005 the British firm Intelligent Energy produced the first ever
working hydrogen run
motorcycle called the ENV (Emission
Neutral Vehicle). The motorcycle holds enough fuel to run for four
hours, and to travel 100 miles in an urban area, at a top speed of 50
miles per hour.
In 2004 Honda
developed a
fuel-cell motorcycle which utilized the Honda FC Stack.
In 2007, the Revolve Eco-Rally (launched by HRH Prince of Wales)
demonstrated several fuel cell vehicles on British roads for the first
time, driven by celebrities and dignitaries from Brighton to London's
Trafalgar Square. Fuel cell powered race vehicles, designed and
built by university students from around the world, competed in the
world's first hydrogen race series called the
2008 Formula Zero Championship, which began on August 22, 2008 in
Rotterdam, the Netherlands. More races are planned for 2009 and 2010.
After this first race, Greenchoice Forze from the university of Delft
(The Netherlands) became leader in the competition. Other competing
teams are Element One (Detroit), HerUCLAs (LA), EUPLAtecH2 (Spain),
Imperial Racing Green (London) and Zero Emission Racing Team (Leuven).
In 2008,
Honda released a
hydrogen vehicle, the
FCX Clarity. Meanwhile there exist also other examples of bikes
and bicycles
with a hydrogen fuel cell engine.
A few companies are conducting hydrogen fuel cell research and
practical
fuel cell bus trials.
Daimler AG, with thirty-six experimental units powered by
Ballard Power Systems fuel cells completing a successful three-year
trial, in eleven cities, in January 2007.
There are also fuel cell powered buses currently active or in
production, such as a fleet of Thor buses with UTC Power
fuel cells in California, operated by SunLine Transit Agency.
The
Fuel Cell Bus Club is a global cooperative effort in trial fuel cell
buses.
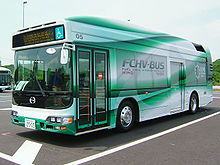
Toyota's FCHV bus at 2005 Expo
The first Brazilian
hydrogen fuel cell bus prototype will begin operation in São
Paulo during the first semester of 2009. The hydrogen bus was
manufactured in
Caxias do Sul and the hydrogen fuel will be produced in
São Bernardo do Campo from water through
electrolysis. The program, called "Ônibus Brasileiro a Hidrogênio"
(Brazilian Hydrogen Autobus), includes three additional buses.
Airplanes
Boeing
researchers and industry partners throughout Europe conducted
experimental flight tests in February 2008 of a manned
airplane powered only by a fuel cell and lightweight
batteries. The Fuel Cell Demonstrator Airplane, as it was called,
used a Proton Exchange Membrane (PEM) fuel cell/lithium-ion
battery hybrid system to power an electric motor, which was coupled
to a conventional propeller.
In 2003, the world's first propeller driven airplane to be powered
entirely by a fuel cell was flown (the first fuel cell powered aircraft
was the Space Shuttle). The fuel cell was a unique FlatStackTM
stack design which allowed the fuel cell to be integrated with the
aerodynamic surfaces of the plane.
Boats
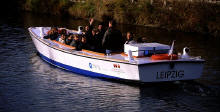
The world's first certified Fuel Cell Boat (HYDRA), in
Leipzig/Germany
The world's first Fuel Cell Boat
HYDRA used an AFC system with 6.5 kW net output.
Submarines
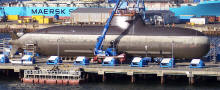
Type 212 submarine with fuel cell propulsion of the
German Navy in dry dock
The
Type 212 submarines of the German and Italian navies use fuel cells
to remain submerged for weeks without the need to surface.
Fueling stations
The first public hydrogen refueling station was opened in
Reykjavík, Iceland
in April 2003. This station serves three buses built by
DaimlerChrysler that are in service in the
public transport net of Reykjavík. The station produces the hydrogen
it needs by itself, with an electrolyzing unit (produced by
Norsk Hydro), and does not need refilling: all that enters is
electricity and water.
Royal Dutch Shell is also a partner in the project. The station has
no roof, in order to allow any leaked hydrogen to escape to the
atmosphere.
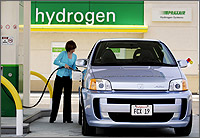
Hydrogen fueling station.
The
California Hydrogen Highway is an initiative by the
California Governor to implement a series of
hydrogen refueling stations along that state. These stations are
used to refuel
hydrogen vehicles such as fuel cell vehicles and hydrogen combustion
vehicles. As of July 2007 California had 179 fuel cell vehicles and
twenty five stations were in operation,
and ten more stations have been planned for assembly in California.
However, there have already been three hydrogen fueling stations
decommissioned.
South Carolina also has a hydrogen freeway in the works. There are
currently two hydrogen fueling stations, both in Aiken and Columbia, SC.
Additional stations are expected in places around South Carolina such as
Charleston, Myrtle Beach, Greenville, and Florence. According to the
South Carolina Hydrogen & Fuel Cell Alliance, the Columbia station
has a current capacity of 120 kg a day, with future plans to develop
on-site hydrogen production from electrolysis and reformation. The Aiken
station has a current capacity of 80 kg. There is extensive funding for
Hydrogen fuel cell research and infrastructure in South Carolina. The
University of South Carolina, a founding member of the
South Carolina Hydrogen & Fuel Cell Alliance, received 12.5 million
dollars from the
Department of Energy for its Future Fuels Program.
Japan
also has a
hydrogen highway, as part of the
Japan hydrogen fuel cell project. Twelve
hydrogen fueling stations have been built in 11 cities in Japan. Canada, Sweden
and Norway
also have
hydrogen highways implemented.
Fuel cell economics
Use of hydrogen to fuel vehicles would be a critical feature of a
hydrogen economy. A fuel cell and electric motor combination is not
directly limited by the
Carnot efficiency of an internal combustion engine.
Low temperature fuel cell stacks
proton exchange membrane fuel cell (PEMFC),
direct methanol fuel cell (DMFC) and
phosphoric acid fuel cell (PAFC) use a
platinum
catalyst. Impurities create
catalyst poisoning (reducing activity and efficiency) in these
low-temperature fuel cells, thus high
hydrogen purity or higher catalyst densities are required.
Although there are sufficient platinum resources for future demand,
most predictions of platinum running out and/or platinum prices soaring
do not take into account effects of reduction in catalyst loading and
recycling. Recent research at
Brookhaven National Laboratory could lead to the replacement of
platinum by a
gold-palladium
coating which may be less susceptible to poisoning and thereby improve
fuel cell lifetime considerably.
Another method would use iron and sulphur instead of platinum. This is
possible through an intermediate conversion by bacteria. This would
lower the cost of a fuel cell substantially (as the platinum in a
regular fuel cell costs around $1500, and the same amount of iron costs
only around $1.50). The concept is being developed by a coalition of the
John Innes Centre and the
University of Milan-Bicocca.
Current targets for a transport PEM fuel cells are 0.2 g/kW Pt –
which is a factor of 5 decrease over current loadings – and recent
comments from major
original equipment manufacturers (OEMs) indicate that this is
possible. Recycling of fuel cells components, including platinum, will
conserve supplies. High-temperature fuel cells, including molten
carbonate fuel cells (MCFC's) and
solid oxide fuel cells (SOFC's), do not use platinum as catalysts,
but instead use cheaper materials such as nickel and nickel oxide. They
also do not experience catalyst poisoning by carbon monoxide, and so
they do not require high-purity hydrogen to operate. They can use fuels
with an existing and extensive infrastructure, such as natural gas,
directly, without having to first reform it externally to hydrogen and
CO followed by CO removal.